In recent years, commercial automation has actually made gigantic leaps. Thanks to technological development, loading devices can currently deal with a wide spectrum of products, from liquids to semi-liquids, from solids to pasty. If only a few years ago, automation in the genuine sense of words was practically difficult to ensure along with any type of production line, today there are makers that can function independently, without the need for constant human guidance as well as at a much faster speed than was the personalized in the past.
The advancement of filling up machines has had ripple effects on both software and hardware. To a mechanical degree, the even more modern filling machines enable an application precision that simply a couple of years earlier was unimaginable. Besides precision, these devices need minimal foodstuff handling, which enables them to maintain integrity, a necessary aspect with strong and semi-solid foods, and also the items’ organoleptic attributes. We are a growing number of seeing filling up makers that make convenience their strength.
This machinery features interchangeable dispensers made in various shapes and consequently with the ability of refining different items, based on the industrial line’s requirements. Along with these flexible makers, there are other versions solely developed for just one sort of product. In the case of mushrooms, fruit pulp, and also various other sliced products, for example, the honesty of the dealt with foods should constantly be ensured. In these instances, handling precision needs to be absolute, something that is just possible if the mechanical components, as well as the digital “mind” of the maker, are completely stabilized.
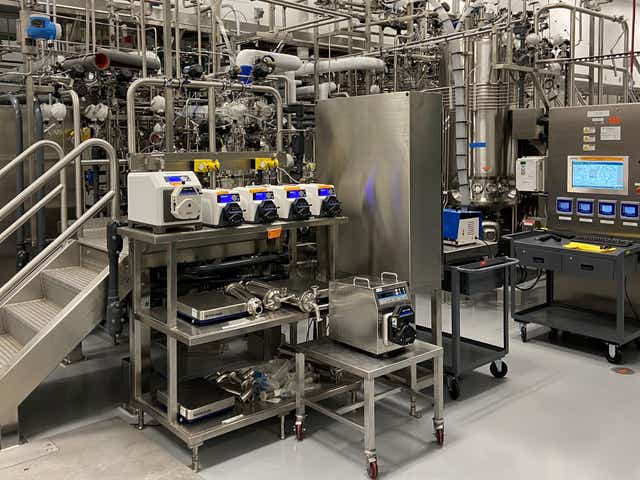
The variables at risk go to the very least 3: volume of the item being dealt with as well as of the container; belt conveyor speed; a variety of dosing cycles per container. Modern equipment permits drivers to change all these parameters through extremely intuitive HMI. The maker’s manufacturing per hr depends upon all of the above-mentioned criteria.
For instance, the rougher the product, the greater the yield. Container dimension is a critical parameter: certain machines can ensure an hourly production of 1,000 or more devices for semi-dense products dosed in containers with a volume from 2,000 to 5,000 millimeters. Performance grows as the container’s quantity lessens: for the very same semi-dense product and also styles approximately 160 millimeters, the per hour yield can also reach heights of 10-12 thousand systems.
An additional really delicate problem with loading makers is their health criterion. There are cutting-edge loading devices currently on the marketplace that permit the operator to automatically set the preferred washing cycle. Equipment that provides this choice does not need special maintenance, except routine jobs on the mechanical parts that a lot of regularly sustain stress and anxiety. It goes without stating that all filling makers readily available on the marketplace have to comply with the most present requirements on health and safety. Learn more info on minnesota industrial coatings by going to this website.
The quality, integrity, and yield of a machine depend upon its maker. Relying on a firm focused on developing a machine for the food industry is not simply simple recommendations, but instead an essential guideline: there are numerous services that concentrate on commercial automation, yet only companies that have solid knowledge in creating devices for the food sector can ensure the customer’s total fulfillment.